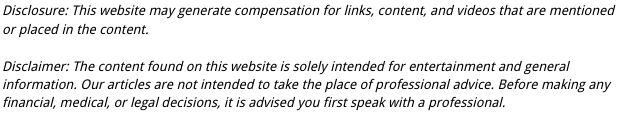
The cost of construction or expansion of a facility with multiple enclosed environments can be intimidating. Manufacturers in particular typically need separate spaces for many of their operations: an inplant office, clean rooms, or warehouse partitions for painting areas. Modular offices and warehouse partitions, built and installed with prefab/modular construction processes, can save a great deal of money and satisfy LEED and green building requirements.
The most popular applications in 2011 for an inplant office and other modular construction were healthcare facilities (49%), dormitories and other college buildings, and manufacturing facilities (42%). It’s estimated that 90% of engineers, 84% of contractors, and 76% of architects have used these components.
Here are four reasons why this practice makes sense.
- Cost and energy savings. According to estimates by the Building Industry Association of Philadelphia, construction costs can be reduced by 9% to 20% when contractors opt for prefabricated offices. Energy consumption during the building process can drop by around 67%, and occupants can see a reduction in energy costs later on.
- Flexibility. Building professionals can choose between two types of inplant office:
- Permanent modular offices and other types of units enable construction companies to complete projects with higher efficiency than traditional onsite construction. The building only needs to be installed onsite.
- Relocatable fabricated units are ideal for applications that need a temporary space for onsite operations quickly, and they can be reused. This includes movable warehouse partitioning systems in case the manufacturer wants to relocate machinery or processes. Many of these can be reconfigured later on and customized with different finishes.
- Time savings. Faster construction means a facility can be up and running sooner. Prefabricated office space, 60% to 90% of which is already completed when it arrives, means speedier construction times while still maintaining quality. It only took one Chinese modular construction company 19 days to finish a 57-story building.
- Waste reduction. Choosing a modular inplant office or prefabricated warehouse partitions helps companies be environmentally responsible. Modular construction can reduce 90% of waste materials generated onsite (cement, plasterboard, shrink wrap, etc.), the UK-based Waste and Resources Action Programme (WRAP) states. And many modular manufacturers have stepped up to meet green initiatives and LEED Indoor Environmental Quality standards.
Manufacturers aren’t the only ones embracing modular construction, either. Schools and residential home builders have jumped on the bandwagon, particularly in terms of energy efficiency, and it’s becoming increasingly popular for hotels. In 2017, Marriott International announced its intention to expand modular construction in its developments. Both the market and the drive for this type of construction seem poised to continue long into the future.