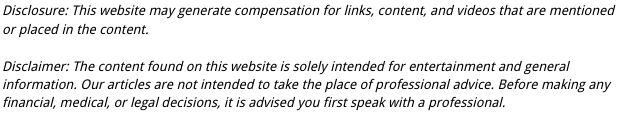

Globally, the printed circuit board (PCB) market was nearly $60 billion in 2012, showing real growth of 1.7% of the previous year, according to the World PCB Production Report for the Year 2012 as published by IPC. PCBs are one of the central concepts of electronics.
The first PCBs involved large electronic components which were mounted on wooden bases and connected with metal strips or rods. Over time, metal frames took the place of the wooden bases and wires connected to screw terminals replaced the metal strips. With this shift came the ability to make far smaller PCBs. Understanding PCBs and prototype PCBs begins by understanding the steps that go into PCB creation. From design to fabrication and assembly.
Prototype PCB design
When designing a printed circuit board, the first task is determining where you’ll place the components. Each PCB is designed under its own specifications to be fit into a designated space. Computer-aided design software can be used to map out how the circuit design will fit the board, laying out spaces between electrical paths that may be less than 0.04 inches, or 1 millimeter. This is also when a designer will lay out the location of the contact points and holes for the component leads.
After a circuit pattern had been designed, clear plastic is used to print a negative image of the exact size. In this image, the areas which won’t make up parts of the circuit board appear in black while the actual circuit patter will show up as clear. From this design, instructions can be made for use during the manufacturing process.
Prototype PCB Fabrication
Fabrication is the term used to describe the assembly method PCBs undergo. This is when the layers of the PCB will be pieced together in accordance with the surface design. Once you have the schematic diagram, you can begin fabrication. Layers of fiberglass sheet are laminated with copper patterns that are then used to mount components for packaging.
Laminates can be as large as 4 feet in width and 8 feet in length. They’re made by curing layers of cloth or paper with thermoset resin under pressure and temperature. The result is the formation of an integral piece of uniform thickness.
Fabrication can either be done in-house or contracted out to a third party specialist.
Prototype PCB Assembly
There are two assembly methods of electronically connecting the components of a printed circuit board: Surface Mount Assembly and Through Hole Construction.
Through Hole Construction
Through Hole Construction was the first assembly method used on PCBs. It was patented in 1961 by the American firm Hazeltine. At the time, the development of Through Hole Construction enabled much more complex boards to be created with components fitted far closer together. Electronic components are mounted with wire leads that pass through holes on the side of the circuit board. These leads are then soldered onto copper traces on the opposite side of the board.
Through Hole Construction can be used for single or double-sided PCBs. The leads can also be bent at 90 degree angles in the same direction to enable horizontal installation of the Through Hole parts. The leads can be soldered manually or with the use of a wave soldering machine.
Dating back to the second generation of computers produced in the 1950s to when Surface Mount Assembly took over in the 1990s, Through Hole Construction was the way virtually every component on a prototype PCB board was assembled for most of the 20th century.
Surface Mount Assembly
Surface Mount Assembly was first developed in the 1960s but wouldn’t become widely used until the last decade of the century. With Surface Mount Technology, the components of the prototype PCB were redesigned to provide small tabs or end caps which would be soldiered onto the PCB’s surface. This removed the need for wire leads to pass through the holes as in Through Hole Construction. It also enabled smaller PCB assemblies with higher circuit densities as the component parts shrank and were placed on both sides of the board. Skilled technicians can solder parts as tiny as 0201 packages which are .02 inches by .01 inches. Suface Mount Assembly is generally used with bulk wave soldering or reflow ovens for high volume production. See this link for more.