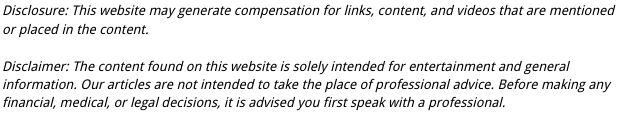
The right machine parts can help you keep operations in your factory going perfectly well. That’s why you should shop for the right parts that are of good quality in order to make some savings. When you do this, you can save yourself the major hassle of replacing parts.
If you need a service like professional camshaft regrinding, it’s best to enlist the help of a verified professional. The same goes for when you need to get a cut camshaft or you want a camshaft and lifter kit, or even simply a camshaft rod. You’ll make your factory a lot safer when you keep your machines in good shape, so it’s worth the time, money, and effort it takes to do so.
Finally, learn about things like a driveshaft vs a crankshaft and other details. This information can help you to pick the right machinery and find the relevant professionals to help you keep it all in shape. With some effort at the beginning, you can get into the habit of maintaining your machines as you need to. When you do, you can work a lot more efficiently and get the best outcome from your machinery.
The United States is home to a vast and diverse manufacturing sector, producing everything from furniture to books to cars to household appliances. This industry employs millions of Americans, and even if it stood alone, the American manufacturing sector would rank among the world’s top economies. All of this is made possible when factories and workshops big and small order the right parts and supplies from wholesalers, as a factory needs more than big and impressive machinery to run. Drills bit cabinets or diamond drill bits may be ordered, along with chuck sleeves or ER20 collets. A similar concept is end mills, and end mills can drill straight down and also through other vectors for flexible work. Along with end mills and drills, a factory’s management may also order carbide grinder parts and even machine lube to keep factory equipment running smoothly. These end mills, drills, grinders, and more make a hard day’s work possible.
Drilling
Drills are technically cutting tools, and many factories and workshops make good use of drills of all shapes and sizes during a hard day’s work. In fact, some 84% of surveyed contractors reported that their most commonly used power tools are power drills in particular. Drill bits can remove material from wood, metal, and more to create holes, nearly always by means of circular cross-section. A drill’s teeth will not only remove material, but also send up these scraps and eject them elsewhere to keep the hole clean and clear. Drills may make holes in a final product to allow air, wires, tubes, or screws to pass through, and drilling is a category of machining (along with cutting and welding). End mills can cut in all different directions, unlike drill bits, which only go in the axial direction. Some manufacturers may make use of both drills and end mills alike. These bits can be reinforced with chuck sleeves to secure them and hold them steady during work, and drill bits may also need proper lubrication during work. A worker may also keep a cabinet or case to keep all their drill bits sorted and organized for convenience during work.
Carbide Grinders
If drills, saws, and welding torches start the process of machining a piece of metal, then carbide grinders finish it. Lathe tables are very important, as they can remove the upraised imperfections on wood or metal known as burrs. The idea of lathes dates back to ancient Egypt, though today’s lathes are tables that run on electricity. After a piece of metal has been drilled, cut, or welded, it may have these upraised imperfections, and those burrs may scrape or scratch other surfaces during the device’s use, or they may even attract static electricity. At the very least, these burrs look ugly and sloppy on a finished product.,
To use a carbide grinder, a worker will place a piece of wood or metal in the lathe table’s assembly, then that assembly will slowly feed the item into a rotating grinder surface. Th RPM of these grinders can be adjusted as needed, and in any case, the rotating surface will simply grind off metal or wooden burrs from the item. This results in a smooth and flawless surface, which is very much desirable. Any modern factory or workshop will have one or more lathe tables or carbide grinders on hand for this very reason, and repair or replace them as soon as necessary.
Machine Lube
Well-functioning machines may be easily taken for granted, but neglecting machine lube and oils may result in disaster. All factory and workshop staff are responsible for applying the correct lube to their machines regularly, and they can acquire these lubes from local wholesalers who offer them. Such lubes are often used to allow metal surfaces to glide easily past each other without friction, but lubes may also prevent surfaces from getting dangerously hot. Other lubes may even prevent rust or corrosion on machines, and some lubes can prevent a buildup of static electricity.
Many factory owners admit that their staff are not always fully trained on lube administration, and many of today’s factory shutdowns are due to improperly lubricated machines shutting down. Diligent training and use of lube can prevent these expensive shutdowns.