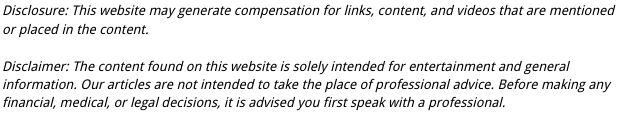
Compressor oil is different from lubricating oil. Lubricating oil provides a thin layer that coats interfacing surfaces. The layer smooths out any imperfections in the surfaces reducing the friction between them. More importantly, the layer provides a cushion that allows the surfaces to slide past each other. Finally, the layer reduces heat generated by friction by reducing the amount of friction and it carries away the heat that is generated so that the surfaces are less likely to warp. As a result, lubricating oil reduces wear, abrasion, and thermal stress.
Compressor oil, like lubricating oil, reduces friction and carries heat. However, in a rotary screw air compressor oil adds another function — sealing. Specifically, seals made from rubber or other solid material suffer from a few disadvantages:
- To provide an effective seal, they must be tight. However, this increases the amount of friction and the amount of energy wasted overcoming the friction.
- Because of the friction created, rubber seals break down quickly.
- Rubber seals can decompose when exposed to water.
- Grit, dirt, or other solid contaminants can deform rubber seals, allowing them to leak.
As a result, rotary screw compressors use oil is to seal the compression chamber. Due to its viscosity, oil is very slow to allow air to escape. This makes oil a very good sealant between air compressor parts.
However, when it acts as a seal, oil is exposed to some extreme conditions that can cause it to break down. Here are three ways compressor oil breaks down and how Purolube Xtend additive concentrate can reduce their effects:
Contamination
When air is compressed, contaminants in the air, such as dust, vaporized chemicals, and water vapor, are forced into the oil. The oil can undergo chemical changes as a result of the contaminants. Compressor oil analysis reveals that these contaminants can react chemically with the oil to produce acids. Although less than 1% of a compressor fluid has turned acidic when the oil reaches its condemning limit for TAN, acidification can substantially reduce compression oil effectiveness.
Heat
Heat can cause long organic molecules in compressor oil to break apart. This can lead to degradation of the compressor oil, but more importantly, can deplete additives intended to keep compressor oil from breaking down. Without these additives, the degradation of the compressor oil is accelerated.
Oxidation
Oxidation is the most destructive contaminant that compressor oil can encounter. Since air contains substantial numbers of oxygen and oxygen ions, the compressor oil is continuously exposed to an oxygen rich environment. Oxygen causes almost continuous acidification of compressor oil.
Purolube Xtend additive concentrate uses ion exchange to pull acid molecules out of the compressor oil. As a result, the pH level of the oil is controlled. This means that compressor oil treated with Purolube Xtend additive concentrate can avoid some of the most destructive forces that compressor oil can face.
Whether degradation arises from heat, contamination, or oxydification, Purolube Xtend additive concentrate can reduce acidification and maintain the integrity of compressor oil.