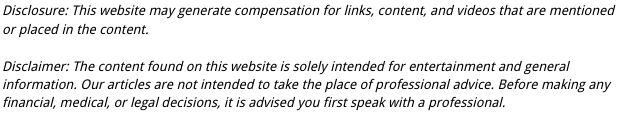
Today’s best work environments are easily transitioned into the most productive spaces. In fact, after years of many companies transitioning to open office spaces, there are a growing number of companies who are working to make sure that the people who need to have meetings have the right spaces.
Finding the right way to use modular office spaces creates the best ways to make sure that the building is working for you. Warehouse offices, for instance, can be a challenge, especially in a factory where there are loud production lines. With the use of the latest modular office options, however, many new locations can be created.
When Was the Last Time You Used Prefabricated Walls in Your Work or Office Space?
Inplant offices are increasingly popular in many places. Even in warehouses where there has never been an office space before, it is possible to use warehouse partitioning systems to create modular offices. Outside of a warehouse, however, there are also many times when a traditional soundproof office can be very helpful. From phone calls that involve contract negotiations to employee conversations about salaries and benefits, there are many times when popular open office spaces are simply not practical.
As more and more companies go back to more traditional offices, it is also increasingly common for these businesses to use prefabricated office walls. This approach helps save money, limit production time, and is good for the environment. In fact, a report by the Building Industry Association of Philadelphia estimates that going modular can reduce construction cost by as much as 9% to 20%. This trend is so effective, in fact, that some of the largest hotels are using prefabricated plans. For instance, Marriott International pledged to use modular construction techniques in 13% of its North American developments in the year 2017.
Consider these facts and figures about the many times when modular offices and other kinds of prefabricated construction materials are used:
- In addition to reducing energy costs later on for occupants, modular constructions reduces energy consumption during the building process by approximately 67%.
- Permanent and relocatable are the two main kinds of modular construction.
- Modular construction can reduce cement, bricks, timber, concrete, wood pallets, shrink wrap, cardboard, plasterboard, and other waste materials by up to 90%, according to UK-based Waste and Resources Action Programme (WRAP).
- Projects can be completed much faster when using these methods since 60% to 90% of all prefabricated construction occurs in a factory or warehouse.
- Modular methods also allow for speedier construction times while at the same time still maintaining quality. For instance, one Chinese modular construction company recently built a 57-story building in a mere 19 days.
- Approximately 76% of architects, 84% of contractors, and 90% of engineers use prefabricated or modular construction processes on at least some of their projects.
Today’s work environments are a dynamic combination of digital off site meetings and in person conferences, as well as traditional warehouse spaces. Making sure that all of these spaces work as effectively as possible often requires the use of prefabricated walls and modular offices. Fortunately, these predesigned materials are often less costly, faster to construct, and more environmentally friendly.