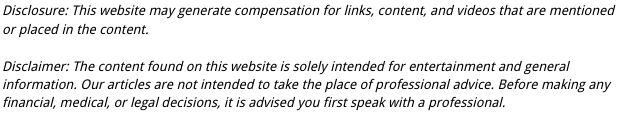
For liquor brewers, the use of barrels is not expected to fade out soon. This has been considered as the best liquor storage equipment that has a vast load of benefits. The barrels are distinguished from the size and material used to make them as well as their quality. Below are different ways that you can assess the storage equipment before purchase.
Understanding the size of the barrel to purchase is very important. This is helping to facilitate the product to be stored. The quantity of wine you opt to keep will answer the question, how big is a wine barrel?
You can come across many wooden barrels for sale on the internet. This is why choosing the best material for the storage equipment should be done. The kind of length and breadth used during barrel machining should determine its positioning. Making evaluations on different types of barrels helps one settle on the best.
There is much that you should be informed about cask construction. This is because there may be differences in making wine and whiskey barrels. For example, when making whiskey barrels, the best material should be used since it may influence whiskey’s quality stored in it. The barrels are made with different specifications to ensure they meet the product’s standards to be kept.
If you’re looking for a good surface finish and are using barrel finishing, you’re likely aware that the quality of your finish is going to depend on your use of tumbling drums, polishing agents, lubricating agents and carrying agents.
What is barrel finishing or barrel tumbling? It’s an operation which takes a mix of media, parts and compounds to perform surface improving operations. This operation is performed in a barrel or tumbling drums and then rotated at a certain speed (usually about 28-32 RPM). While the barrel is rotating, the mix is rounded at the corners and grinding, descaling and other processes occur.
There are many benefits of using tumbling, tumblers and tumbling drums:
- Many parts can be processed and finished at the same time
- Parts can be finished much easier than if they were done manually
- Finished parts come out strong and tougher after being finished
- The tumbling process gives finished parts an amount of stress relief
You can save a lot of time tumbling by doing careful machining of parts. Depending on the amount of material you’ll have to remove from parts, the tumbling process in tumbling drums usually takes anywhere from 6 to 24 hours.
It’s important to note that with barrel finishing, there are two different processes: wet tumbling and dry tumbling. Dry tumbling is used for all phases of working with parts including finishing and wet tumbling is typically used to remove excess stock.
In wet tumbling, barrels are used that are composed of different materials and typically horizontal barrels are used. If these barrels are being used with fragile parts, the barrels are typically spun at slower speeds to prevent damage to the parts. The wet part of wet tumbling comes when water is added to the barrel after the parts and media are loaded. Less water equals a faster cutting rate whereas more water equals a slower cutting rate and a finer finish.
In dry tumbling, a horizontal barrel is also used and can be double-decked to save floor space. Rather than water, elements like grit from corn cobs and walnut shells are used to smooth out parts. This helps speed up the cutting process, but won’t fracture the parts.
There are plenty of benefits to be gained from both wet tumbling and dry tumbling and what sort of finish you’re hoping to get out of your combination of parts and media. To figure out which process works best for your needs, determine what you’re trying to accomplish and decide whether wet or dry tumbling will best get the job done.