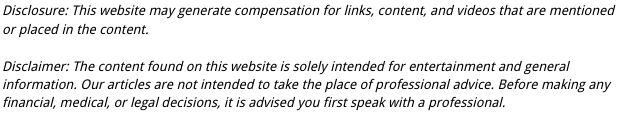
Are you an inventor that has finally invented something that you believe will change the world? If that’s the case you have done a lot of work to get to this point. More than likely you have made extensive drawings and blueprint detailing how the item will work and you have probably even decided what the product will be made of. Once all of those steps are done it is time to talk to manufacturers. If your invention has metal components you are probably starting to hear terms such as induction hardening that are completing unfamiliar to you. If that is the case let us define some of those terms for you.
Induction Hardening
Induction hardening is the process by which the surface of an alloy or steel component is hardened. All parts to undergo this process are put in water that has been cooled by a copper coil. They are then heated higher than the temperature required for transformation. This is done by applying a different current to a copper induction heating coil. The interchanging currents create a vacillating magnetic field in the metal piece. This is done into the appropriate depth of hardness is reached and then the metal piece is plunged into oil or the appropriate cooling agent. Usually done in an induction forge, this process is most often used with steel or copper alloy parts. You choose this method if your parts are bearing races or threaded pipes.
Case Hardening
Case Hardening is used when large pieces can be hardened in batches, instead of individually. In this instance, the metal is hardened using carburization. The steel is heated above 880 degrees celsius then coal is put into the piece so that the outside of the item receives more carbon, while the carbon density stays the same in the middle of the piece. After the carbon is applied the piece hardens.
Induction Flame Hardening
Induction flame hardening is not that much different from induction hardening. In this case, an oxy-acetylene flame is used to heat the surface of the piece being hardened. The surface is heated higher than the transformation temperature then is it sprayed with water. This creates a hard surface layer. In order for this to work the piece must have carbon levels greater than .35%.
Overall you do not need to become extremely educated about how your parts of manufactured. No one expects you to learn all about induction heating equipment and induction melting, however, if it is best to become somewhat knowledgable about the process and how your parts will be manufactured. This will make sure you are choosing the best possible process and can guarantee quality products for your customers.