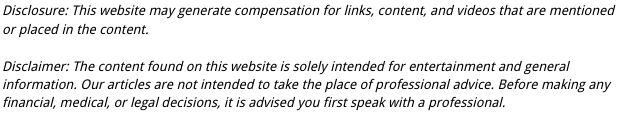
If you use a kiln or forge on a regular basis, it is likely that you already understand the challenges that can be involved in operating these instruments properly. A kiln or a forge can be used to create high amounts of heat and can be used for multiple applications like pottery design, ceramic design, glassblowing, or blacksmith work. If you are involved in any of these occupations and already operate a kiln or a forge, you would know that due to the significant amounts of heat generated by these devices, there can be a lot of wear and tear over time. In fact, these require regular maintenance and replacement of parts to keep functioning at optimal levels. From controlling gas consumption to making sure that firing times remain reasonable for you to work properly, there is a lot to take care of if you operate a kiln or a forge. There are, however, certain ways you can make things a lot easier for yourself.
For a number of applications which require a lot of heat output, professionals would typically use something like a kiln or a forge. These devices are used mostly in applications like metalworking, pottery, working with ceramic, and glass blowing. The main problem with generating this much of heat is that the components of the device tend to get affected quickly by wear and tear. Regular exposure to this much of heat can cause damage if you are not careful and if you do not maintain your equipment properly. The average kiln can create a temperature anywhere from 1800 to 2400 Fahrenheit and the kiln elements will typically last anywhere up to 100 firings. These kiln elements need to be regularly changed and it is recommended to do so when the resistance has increased to 9%. However, there is a lot you can do by introducing different kinds of thermal insulation coatings into your kiln. This is where ITC ceramic coatings can really come in handy.
The use of ceramic insulation coating has been in vogue in many industrial applications that have to deal with high heat for a long time. The main reason for this is the fact that ceramic has incredible heat-resistant qualities and can easily withstand temperatures close to 4000 Fahrenheit. ITC ceramic coatings which are specially formulated for high heat applications can even withstand up to 5000 Fahrenheit. This makes ITC ceramic coatings one of the best things you can possibly use if you want to protect certain parts of your kiln or forge from exposure to high heat. Implementing some kind of high temperature ceramic coating in these devices can really increase the overall lifespan of the components inside and can give you the peace of mind knowing that you will get much more use out of this very important part of your workflow.
Overall, if you are indeed working with a kiln or a forge on a daily basis, considering the application of something like ITC ceramic coating is something that you can definitely think about. This can improve your workflow significantly and provide you with much more efficient and long term use of your important kiln or forge.