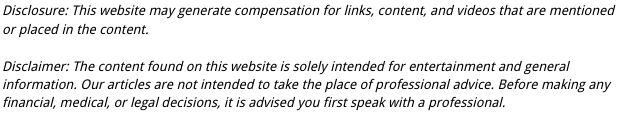
For many thousands of years, metals of all sorts have been used to make tools and weapons alone, and in fact some periods of history are named after the most commonly used metals of the time. The Copper Age, Bronze Age, and Iron Age are fine examples of this, and such metals and more are widely used today, too. But of course, today steel and aluminum are used to make more than swords or field plows. Combined meals of brass and copper, and other composites, form alloys that are very useful in some applications where other metals would fail. Thin metal strips such as thin steel sheets or thin aluminum strips can be bought wholesale, and a factory owner may search “metal sales near me” to find some suppliers. Searching “metal sales near me” may be done by car plants, or a machine shop may seek out “small metal sales near me” or “copper metal sales near me”. How can metals be refined in the workplace, and just how large has the metal industry become?
Metal Production and Sales
Ever since the Industrial Revolution began, the production of metals such as steel and aluminum have grown sharply, and such metals can be used for producing buildings, cars, household appliances, and even weapons of war. In the United States alone, some 138,900 sheet metal workers were employed in 2016, and the U.S. Bureau of Labor Statistics estimates that the metal fabrication industry may grow 9% from 2016 to 2026. This may mean adding another 12,000 jobs to the economy. All of this matches an overall upwards trend of metal production worldwide. Globally, the sheet metal market is due to grow at a continuous average growth rate of 4.09% or so, and that may continue from 2018 to 20222 at the very least. What is more, metals are often recycled, and around 40% of all steel produced in the world today comes from recycled materials. Steel enjoys a recycling rate of 80% or so, very high among all materials that can be recycled.
Using Steel in the Workplace
Who is buying wholesale steel, aluminum, and other metals? Factories and other workshops make good use of these metals, and wholesale suppliers are essential to keep production running. Large factories and small workshops alike need metal, and they may ask for steel, aluminum sheets, copper or brass, or even alloys for specialized work.
A foundry and steel mill will create pure steel and form it into useful sheets to sell wholesale, while factory and workshop staff will machine (a verb) that metal into usable products. Machining is the general act of altering metal so that it can be used in a final product, and machining may involve drilling, cutting, welding, and grinding. Drills can create holes for screws, nails, wires, tubes, air flow, and more, and welding combines metals with heated, pressurized gas like nitrogen and helium. Cutting may be done with physical saws, or even performed with laser heads. It may sound strange at first, but lasers are in fact very effective cutting tools, even when used on metal. Light energy, once concentrated into a narrow beam, puts out enough energy in its narrow field of effect to melt cleanly through metal and plastic. What is more, laser cutting is cleaner and more precise than any physical cutting tool, and despite the beam’s intense heat, that energy is concentrated. Thus, there is no collateral damage such as melting or warping to nearby materials when metal is cut with lasers.
What about grinding? Once a piece of metal has been machined, such as from cutting or welding or drilling, there may be upraised imperfections, known as burrs. These burrs may scratch and scrape against other surfaces when the finished product is used, and burrs may also attract static electricity. So, a factory or workshop will feature lathe tables, which offer a rotating grinder surface to grind off those burrs. The RPM speed of the grinder can be adjusted, but in all cases, an assembly will hold the piece of metal steady and move it toward the grinder surface, or “feed” it. In this way, burrs are ground off and the metal’s surface is smooth and flawless, ready for the final product.