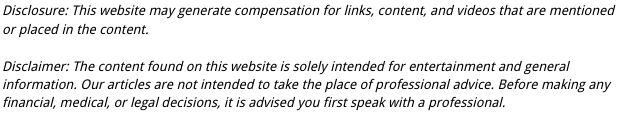
We are living in a time when businesses, schools, churches, and many other groups are rethinking their spaces. In fact, as the Centers for Disease Control (CDC) most recently published its guidelines for how schools will be allowed to operate in the fall, there are many school districts completely rethinking the ways they will use their available spaces. With recommendations to keep fewer students in a classroom, for instance, schools are left with two choices: create a schedule where only have the students attend at a time or double the amount of classroom space that is available. The only way to offer the increased amount of space and prepare it during the next few months will be to make use of the latest modular and prefabricated offices. Transforming these structures into an educational setting has several advantages.
From providing new spaces that are easier to keep clean and sanitized to using prefabricated office walls to create the necessary social distancing requirements means that educators can meet the required safety guidelines while still providing areas that can bring learners together instead of only seeing each other on a screen.
Modular Warehouse Offices and Other Kinds of Prefabricated Offices Provide Options for Many Platforms
Fortunately, the prefabricated offices industry is already thriving. Using already designed materials to answer the needs of school districts and other groups, the prefabricated offices industry may find itself in even higher demand. When school boards realize that they need to find more space so they can accommodate learners, for instance, they will likely have to make plans for additional spaces. Warehouse partitions that have been mainly used for those work setting purposes may soon become barriers that create two rooms out of large community spaces in schools.
No one knows exactly what school will look like when classes start again in the fall, but it is likely that many superintendents and school boards will need to look at different and new kinds of space utilization.
Consider some of these facts and figures about the many ways that warehouse partitioning systems and modular techniques are used today, and imagine how they might be transformative in the way schools and other agencies move forward:
- Modular constructions reduce energy consumption during the building process by as much as 67% and reduces energy costs later on for occupants. These savings will be key as schools work with already determined budgets to create new spaces.
- Already by the year In 2011, prefabricated and modular construction was particularly popular for certain commercial applications. For example, 49% of respondents used these processes for healthcare facilities, 42% used them for dormitories and other college buildings, and 42% used these methods to construct new manufacturing facilities. As colleges strive to offer an in person educational experience, the need for modular construction of dormitories may be especially important.
- Modular construction can reduce waste materials, according to UK-based Waste and Resources Action Programme. Offering a way to reduce the waste of cement, bricks, timber, concrete, wood pallets, shrink wrap, cardboard, and plasterboard by up to 90%, is going to be equally important to hospitals, schools, and colleges, as it has been to businesses in the past.
- Modular construction was already becoming increasingly popular for hotels. For example, Marriott International pledged to modularly construct 13% of its North American developments back in 2017. These cost and energy savings techniques will be a useful advantage to school districts and other groups who are having to rethink how spaces care used.
- Permanent and relocatable are the two main types of modular construction. there is some research that indicates that both of these types will be needed as businesses and schools alike rethink the way they will provide their services.
- Projects can be completed much faster when using prefabricated methods, since 60% to 90% of all this construction occurs in a warehouse or factory. The speed of these options will be essential as many businesses and schools need immediate space solutions.
- Before the pandemic, as many as 90% of engineers, 84% of contractors, and 76% of architects used prefabricated or modular construction processes on at least some projects. That number will likely increase as new safety concerns emerge.