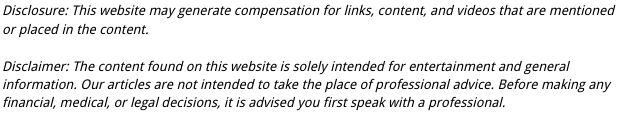
Vacuum induction furnaces are vital in the smelting of alloy steel, precision alloys, and high-temperature and electromagnetic materials. The induction furnace smelting equipment is energy-efficient, flameless, and rapid in smelting. But like most other foundry processes, the induction furnace smelting process may get faulty and compel you to find a quick solution to get you back to work. Well, worry no more!
This blog post will present to you some of the three common induction furnace process problems and their quick fixes.
Slag Ring Problems that Occur in Vacuum Induction Melting Furnace
Slag ring problems are caused by the high gas content in the molten steel or the continuous splattering process of the molten steel. When the molten steel from the furnace’s crucible splatters continuously in the smelting process, slag rings form within the molten material. Sometimes these slag rings appear when you try to pump out excess gas in the molten steel. The outward movement of the gas from liquid steel can cause slag rings in your molten material.
What Is the Solution for Slag Rings?
You can correct the slag ring problem by using three methods. First, for large slag rings, you can break the vacuum by direct welding because the weld with the crucible is firm. Second, you can iron out the slag ring by adding extra loading amounts and tilting your equipment back and forth during the washing of the furnace. Third, you can treat the slag rings that have already left the arc by use of a feeding basket.
Induction Melting Furnace Spray Problem
The spray problem in induction furnace smelting is caused by two primary reasons. The melting speed of the material in the furnace is one of the leading causes of this problem. If a large and somehow cool part of the liquid or semi-liquid metal deeps to the bottom of the crucible in a sudden manner, then that falls into the hot molten pool at the bottom of the crucible and may cause spillage.
The spray problem may also occur when you’re adding some alloy material. The addition may create the generation of high gas content and spillage in some cases.
So, How Do You Solve Induction Furnace Smelting Spray Problems?
You should use the right power supply system to provide proper power supply for even melting that prevents the bridge condition, which, when broken by some molten material, deeps to the bottom of the crucible to cause spillage. You can also avoid the problem by cooling down the system after a splash. You should slow the reaction and let the melting and boiling slow down.
If a large splash occurs, you can pump some Argon gas into the furnace to reduce the vacuum caused by the process and increase the pressure within the void. You can later continue pumping out the gas after the molten material calms down.
The Bridge Problem in the Induction Melting Furnace Smelting Process
The bridge smelting problem occurs when the induction melting furnace material is too massive. The problem may also occur when a carbon monoxide plate is added to carbon monoxide steel at a later stage during the smelting process. The two can weld at the melting point, but the slag ring may become too large to bridge.
What’s the Solution for the Bridge Smelting Problem?
You can use a hammer to break open the material, or you can adopt a broken vacuum to solve the problem. You can also iron the bridge site by tilting the crucible, and the molten steel liquid flow can smooth the bridge site.
Approximately 17% of American steel imports are from Canada. The Canadian steel industry is vast, and it uses many vacuum induction furnaces in the steel melting process. If you’re running a steel smelting foundry, then you’re most likely to encounter the three cited induction melting furnace smelting problems.
You need not worry about them if you can follow the recommended quick fixes because they can help you to end these common smelting problems.