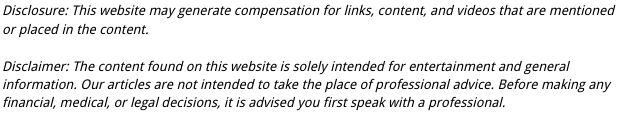
What Is Injection Modeling?
Injection modeling is a manufacturing process that produces parts in large volume that is typically used for mass productions processes, making thousands and even millions of times in, succession. Injection molding is used because its ability to scale production on a mass scale—its initial costs are per unit during the manufacturing process is very low and tends to drastically decrease as more parts are produced in bulk to meet demand. Injection molding is so popular because of efficient process, RIM (Rim Injection Molding) is an intricate process which molded polyurethane parts are created. During the process, two liquids components are mixed and injected action. Injection molding produces meager scrap rates like the traditional manufacturing process, but also produces waste plastic that comes from consistently from 4 different areas: the sprue, the runners, gate locations, and other overflow materials that leak from the overmolding process. The recommended wall thickness for a RIM molded part for solid materials is typically 1/8 inch, but sections sometimes have walls as thick as ½ inches that can be successfully molded. The benefits of injection molding are its high level of repetition—injection molding is similar to injection molded enclosures that are an idea for brand consistency and part reliability in high volume production.
What’s The Difference Between Structural Foam Molding vs. Injection Molding?
Injection molding is highly important for manufacturing processes for decades—the process is used to make a wide range of products on a mass scale. Many manufacturers and product developers benefit from the uses of injection molded enclosure for its variety of parts, components, and products but there many people who don’t know the difference in different types of molding is structural form molding. However, knowing the specifics of this process and how it varies from other types of injection molding.
1. Structural form molding: When undergoing the structural foam molding process, an inert gas is added to a melted polymer and injected into an encapsulation molding process. The gas forces the melted polymer into the mold, creating a uniform thickness throughout the mold that eventually forms an unbroken skin against the mold and a honeycomb structure that develops to form its inferior structure. The honeycomb structure prevents shrinkage, allowing manufacturers to reduce product weight without compromising structural integrity. People tend to choose structural foam molding over traditional injection molding because of its increased strength, improved aesthetics, and more molding options. The honeycomb structure has a very high strength-to-weight ratio for parts and products than traditional tactics; molds are more resistant to impact and have a variety of applications (I.e., concrete, sheet metal, fiberglass, and even wood). Its structural molding results in thicker and intricate parts and components without creating depression or sink marks—low-pressure process reduces stress and warpage issues that leave a desired texture. Molding options are available in lesser traditional designs because of its process; they’re less expensive to make and long-lasting because they don’t undergo a significant amount of pressure.
2. Reaction Injection Molding: RIM is a low-cost tooling process aimed towards high-quality Polyurethane and Urethane plastic parts with class A surfaces. RIM utilizes a polyurethane injection molding process that RIM tooling is made from aluminum because it’s a lower cost than other plastic manufacturing methods. However, depending on the variety of raw materials available, architectural detailing, painting and finishing requirements—injection molding has diverse functions and project freedoms that allow more designers and OEM’S to utilize the traditional RIM process as their preferred method.