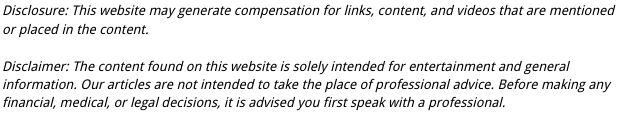
In the commercial food business, such as dining, farming, and factories, there are many machines that are essential to the day to day operations. One of such items is the industrial food crusher, which breaks up a variety of materials, including food. Here is everything you need to know about food crushers and their important parts.
One: a rotary crusher is typically built with shaft impactors inside it to generate considerably larger force than other designs of food crushers. These rotary crushers are perfect for food processing and recycling material such as carboard. They have a wide possible range of size reduction ratios. The speed of this rotary can vary from 85 revolutions per minute all the way up to 1,200 revolutions per minute, depending on the model.
Many models of food crusher have tumbling drums attached. While these barrel-shaped tumblers can vary widely in diameter and length, it usually is tube like in shape, meaning that the diameter is smaller than the length. The barrel can rotate at anywhere from 20 to 38 revolutions per minute, depending on the size of the tumbler and the contents placed inside it. These drums usually have a metal skin and a hardwood lining inside the barrel, which needs to be replaced on occasion.
The tumbler on a food processor is very sensitive to over weighted loading or improper loading. The amount of product that can be safely fit into the barrel is determined by the barrel size, the size and consistency of the contents, the content’s fragility (is it vegetable compost or is it meat bone?), and the content’s shape and weight.
The tumbling barrel should not be loaded at less than 45% of capacity, or more than 60% of capacity. This sensitivity just shows how important proper loading of the barrel is. The optimum capacity for best results is 50%.
Dryer food product and wetter food product should be processed separately for the best, most efficient, and most consistent results.
Many modern models of industrial food crushers have at least six different teeth configurations, wich can customize the speed and consistency of which your crusher achieves results. It also broadens the materials that you can process in the crusher to chemicals, salt, and fertilizer materials.