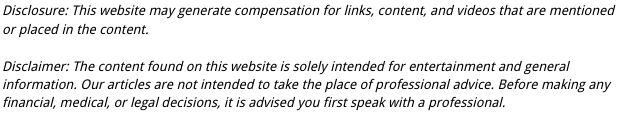
The modern American manufacturing sector is truly enormous, contributing an incredible $2.17 trillion to the American economy and employing 12.5 million people across the nation. For every dollar spent on manufacturing, $1.40 is added to the economy, and everything from household appliances to cars to weapons of war are being made. But there is more to manufacturing than conveyor belts and hammers; the right tools are always needed for the job, and some are highly specialized and advanced. Take, for example, PCD solutions (polycrystalline diamond) tools, which are hard enough to drill through just about anything without breaking. PCD tools like these are thus in high demand for machining metal and wood, and let’s not forget about roller burnishing tools and lathe tables, either. All of this and more can make the manufacturing process smooth and easy.
PCD Solutions Done Right
A drill bit can be made of ordinary metal for low-stress jobs, but sometimes, a factory is going to need some PCD solutions to drill through hard metal repeatedly. How are they made? To make PCD solutions possible, ground-up diamond grains are melded into a hard coating on a drill bit, and such a drill bit boasts extraordinary toughness and thermal resistance for even the most demanding jobs. These PCD solutions allow for drill bits that last much longer than ordinary ones, and some bits can drill through 9,000 feet per minute with such diamond coatings. Even abrasive materials can be drilled easily, such as plastics, rubber, graphite, and others, and a good workshop or factory will come fully stocked with a set of different drill bit models. A factory or workshop owner can find local wholesale suppliers who offer such kits, and order replacement drills as needed to maintain a full inventory. The manufacturing process will grind to a halt if drilling can’t be done.
Roller Burnishing
The term “machining” refers to cutting, drilling, and welding metal and similar materials during the manufacturing process, but other steps must be taken before a product is ready to leave the factory. Roller burnishing is a good example, and it concerns an object’s metal surface. Metal is tough, to be sure, but roller burnishing can improve it. A roller burnisher tool features a hard, round surface that is rubbed all over the object, applying firm but even and smooth pressure that will slightly and evenly compress the metal. This improves the metal’s endurance and strength, which is vital, and even a used object can be sent to a workshop for some touching-up burnishing. That is, a given metal object can be burnished more than once if need be. It’s aesthetic, too; burnishing can give a metal object a shiny, smooth, glossy surface that is attractive to the eye and to the touch, which will impress customers and make a good impression. For these reasons and more, many products are advertised as having thoroughly burnished surfaces on them. This even includes jewelry.
Using a Lathe Table
The machining process is an imperfect one, and after some cutting, drilling, or welding is done, the object has some flaws on its surface. This is normal, but it must be dealt with. Metal, wood, plastic, and other materials will have rough, upraised imperfections called burrs, and they can be a real problem if they’re not removed. Burrs are unsightly and will make a bad impression on customers, and of course, burrs can scratch and scrape up other objects or surfaces while the item is in use. Metal burrs can attract static electricity, and short out electrical components.
So, a lathe table is used, which features an assembly that holds the item, as well as a rapidly rotating grinder surface. As the object is slowly fed to that grinder, the grinder scrapes off all burrs and leaves a smooth surface, and this can be done for any an all burrs on the object. Care should be taken, though, so the grinder doesn’t go too far and damage the object. That grinder can also have its speed adjusted for different jobs, and lathe tables tend to be finely controlled with computers for precise and smooth work. Once that is done, the object is ready for further work, such as roller burnishing or painting.