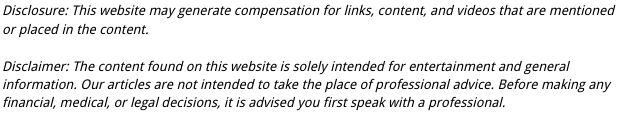
In any business landscape, it’s a given that supply chain constraints can pop up like unexpected hurdles on a race track. But have you ever wondered how top businesses stay in the lead despite these setbacks? They employ innovative strategies, transforming constraints into opportunities for refining their operations. This rewarding journey is what we’re about to unpack here. Buckle up as we dive into how these industry leaders turn constraints into stepping stones toward greater efficiency and profitability.
The Benefits and Detriments of a Global Supply Chain
A global supply chain can provide significant advantages to businesses, particularly in terms of cost efficiency and market expansion. Utilizing a global network of manufacturers and suppliers allows companies to harness the expertise and low-cost production capabilities of different regions. However, it’s not a rose-tinted picture all the time. Globalization can often mean that these supply chains are spread thin, susceptible to disruption from factors out of their control, like geopolitical turmoil or unforeseen pandemics. Debris shields, which act as protective measures in many manufacturing processes, can also become a supply chain constraint if there’s a global shortage or logistical difficulties.
The detriments of a global supply chain can be far-reaching. Supply chain constraints can result in delayed deliveries, increased costs, and a consequent dip in customer satisfaction. A major constraint, as mentioned, could be the unavailability of essential components like the one mentioned above. This could cause significant delays in production lines, potentially leading to financial losses and damaged business relationships.
Despite the challenges, businesses that effectively manage these constraints can position themselves for greater success. It’s often through overcoming these hurdles that companies refine their operations, making them more robust and resilient. The trick is to anticipate potential setbacks, develop contingency plans, and constantly keep an eye out for innovative strategies.
Streamlining Manufacturing Processes
In the pursuit of business efficiency, streamlining manufacturing processes has been a primary objective. It’s a task that demands innovative thinking, especially when dealing with supply chain constraints. The use of pipeline pigs, for instance, has proven to be a game-changer in various industrial sectors. These devices, deployed to perform maintenance without stopping the flow of products in a pipeline, provide a practical and cost-effective solution to ensure uninterrupted operations.
However, streamlining isn’t just about maintaining operations but also enhancing them. This involves factoring in every aspect of production and identifying potential bottlenecks. For example, the unavailability of pipeline intervention gadgets can become a constraint in itself if not properly managed. Thus, it’s crucial to have a robust inventory management system in place to prevent such issues from arising.
Businesses shouldn’t underestimate the value of adaptability. The ability to pivot in the face of unexpected constraints can make a significant difference in maintaining operational efficiency. Whether it’s sourcing alternate resources or adjusting production schedules, staying flexible and proactive can help businesses stay ahead of the curve and drive their growth trajectory in this rapidly evolving global market.
Preventing Worker Injuries
In the fast-paced world of supply chain management, worker safety should never be taken for granted. It’s a critical component that plays a significant role in maintaining productivity and minimizing downtime. When operations are under constant pressure due to supply chain constraints, implementing effective safety measures becomes even more essential, and it’s here that MHFA (Mental Health First Aid) training comes into the picture. This training empowers employees to recognize and respond to mental health issues, leading to a healthier and more productive workplace.
The beauty of MHFA training lies in its universality, regardless of the industry or job role. It equips individuals with the ability to identify signs of mental strain providing support to their colleagues who might be under significant stress, which is common in supply chain management. It’s also worth noting that physical and mental health often go hand in hand. When workers have the mental resilience to deal with challenges, they’re less likely to suffer from physical injuries due to negligence or exhaustion.
Being proactive about worker injuries goes beyond just training. It involves creating a culture of safety where every employee feels accountable for their own well-being and that of their colleagues. This can be achieved by encouraging regular breaks, fostering open communication about safety concerns, and responding promptly to any reported issues.
Maintaining Safe Facilities
Maintaining safe facilities is a key element in alleviating supply chain constraints and fostering efficient operations. This involves adhering to industry standards, such as ASTM F3010, which guides the design and installation of moisture mitigation systems used under resilient floor coverings. It’s not just about compliance but about creating an environment where safety is intrinsic to the processes and protocols.
The implementation of the standard above brings about a safety-focused culture within the workspace. This standard, when applied correctly, helps to prevent moisture-related issues like mold growth, which can compromise the physical health of employees. This, in turn, reduces downtime and helps maintain a smooth supply chain since the workforce stays healthy and operations are less likely to be disrupted by avoidable workplace incidents.
Ensuring safety goes beyond following standards — it’s about continuous improvement and vigilance. Constantly assessing and improving the workspace for potential risks, training employees to be mindful of their surroundings, and encouraging a proactive approach towards safety can make a significant difference. The goal is not just to mitigate constraints but to ensure that every member of the team can work confidently and securely in their environment.
Prioritizing Facility Maintenance
Prioritizing facility maintenance is non-negotiable in any operation that aims to run smoothly and effectively. Shell liners for AG mills, for instance, require regular inspection and maintenance. These liners ensure the optimal performance of the mills, which play a key role in many industrial processes. Failing to maintain these can lead to operational inefficiencies and, eventually, supply chain constraints.
Let’s not lose sight of the fact that the condition of a facility directly impacts its operation’s efficacy. Regular maintenance and timely repairs can help prevent costly downtime and equipment failures. Maintenance isn’t just about the physical infrastructure; it also involves the machinery and tools used within the facility. When these are well-maintained, it ensures that operations are running smoothly and that constraints are kept minimal.
A well-maintained facility also contributes positively to employee morale and productivity. When workers see that their workspace is maintained with care, it boosts their confidence in their safety and their organization’s commitment to their well-being. It’s clear that prioritizing facility maintenance isn’t just good practice; it’s a strategic move that minimizes supply chain problems and maximizes operational efficiency.
Knowing When to Go Custom
There’s a certain point in operations when off-the-shelf solutions no longer meet the unique requirements of a business. That’s where custom transportation containers come into play. These containers, tailored to your needs, can greatly enhance your logistics processes, offering a higher degree of control and efficiency.
Custom containers can be a potent weapon against supply chain constraints. By having containers designed to perfectly fit your products, you can optimize space and reduce potential transportation costs. This flexibility also means that your products are better protected during transport, minimizing the risk of product damage and associated delays.
It’s important to balance the benefits of custom containers against the cost. Going custom isn’t always the best option for every business. It’s crucial to analyze the nature of your operations, the specific needs of your products, and the projected return on investment before making such a decision. Going custom should be a strategic choice, one that brings substantial value to your operations and contributes to the mitigation of supply chain problems.
Making Repairs Quickly
When supply chain constraints are a concern, the promptness of repairs becomes absolutely vital. Unplanned downtime caused by issues like commercial water damage can cripple operations and put added stress on your supply chain. It’s not just about fixing things fast but also about minimizing disruption to your operations.
Commercial water damage repair, in particular, demands immediate attention. Ignoring this can lead to further damage, more downtime, and increased costs. It’s not just about drying out the area but also preventing mold growth, repairing structural damage, and ensuring the area is safe and suitable for continued operations.
Swift and effective repairs are a key strategy in mitigating constraints in the supply chain. By preventing minor issues from escalating into major disruptions, you’re maintaining the efficiency of your operations and keeping your supply chain moving. When it comes to repairs, time is of the essence.
Robotics vs. Manual Labor
In today’s era of technological advancements, a pivotal question enterprises are grappling with is the choice between robotics and manual labor. Robotics are increasingly being seen as a viable solution to mitigate supply chain constraints. The efficiency, precision, and round-the-clock productivity offered by robotic systems can significantly reduce dependence on the human workforce, leading to quick turnaround times and minimizing errors.
This doesn’t necessarily imply that manual labor has lost its charm or utility. For tasks that require a human touch or where pedestrian traffic coating is involved, manual labor can be irreplaceable. There’s a certain level of craftsmanship, personalization, and quality control that humans can deliver, which may be challenging for robots to replicate.
The choice between robotics and manual labor isn’t a matter of ‘either/or.’ Businesses need to strike a strategic balance between the two, leveraging the strengths of each to address specific operational needs and constraints. As technology progresses, the collaborative efforts of humans and robots offer a promising path for the future of enterprises and their supply chains.
Scaling Up Production Efficiently
When it comes to scaling up production, the task is often easier said than done, especially in the face of supply chain constraints. It’s essential to identify and harness tools and strategies that can promote efficiency without compromising the quality of the output. One such tool that’s proving to be highly beneficial is the 4 way lifting chain.
4-way lifting chains offer remarkable strength and flexibility, making them a versatile choice for a wide range of lifting and handling applications in the manufacturing sector. It’s not just about lifting heavy loads but doing so in a manner that’s safe, efficient, and reliable. This means less downtime due to equipment malfunctions and more time spent on actual production, giving a much-needed boost to productivity.
Simply adopting 4-way lifting chains isn’t a remedy for all the challenges associated with scaling up production. It needs to be complemented with other strategies like lean manufacturing, agile management, and smart use of technology. By taking a holistic approach to addressing constraints in the supply chain, businesses can scale up their production more efficiently, driving growth and improving their bottom line.
Applying Proven Strategies for Success
When targeting success in a congested industrial landscape, it’s crucial to utilize every tool at our disposal strategically. One such critical tool is the industrial pipe valve. This seemingly simple component plays a massive role in ensuring the smooth functioning of various processes within the manufacturing sector. They control the flow of liquids and gases, contributing significantly to operational efficiency and safety. Their role can’t be overstated, particularly in industries where precision and safety are paramount.
The journey towards success isn’t without its challenges. Supply chain constraints often pose significant hurdles, affecting the overall efficiency of production. Delays in supplies, fluctuating costs, and logistical issues can quickly escalate, disrupting the smooth flow of operations. It’s during these challenging times that organizations need to exhibit resilience and adapt quickly, employing innovative solutions to navigate these constraints.
To surmount these challenges, businesses must adopt a holistic approach. This involves not only implementing proven strategies such as lean manufacturing and agile management but also embracing innovative solutions tailored to combat specific constraints. The integration of technology, combined with the efficient use of resources, can significantly improve operations, helping businesses steer clear of constraints in the supply chain and paving the way toward success.
In conclusion, businesses can turn supply chain constraints into opportunities for growth and efficiency. By employing innovative strategies such as streamlining manufacturing processes, prioritizing worker safety and facility maintenance, and embracing the use of custom solutions and technology, companies can overcome challenges posed by a global supply chain. The key to success lies in adaptability, proactive planning, and a balanced integration of technology and manual labor, ensuring businesses not only navigate through constraints but also emerge stronger and more resilient.