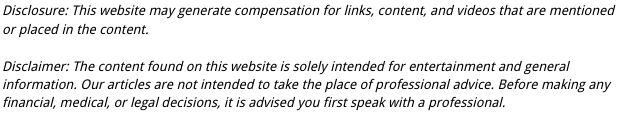
For any industry that relies on manufacturing, nothing can shut down operations down faster than a compressor that’s not performing up to snuff. In order for that not to happen and for operations to continue as normal, there many things companies can do.
One option is to use tools powered with air compressors. In fact, many industries rely on air compressors when it comes to handling materials and especially for spray painting. To that end, many companies use rotary screw air compressors for these jobs because they have many benefits including:
- They are very convenient because they deliver a continuous stream of air, allowing companies to get jobs done faster. Rotary screw compressors are also very safe with very few accidents reported with their use.
- Rotary screw compressors also function in all conditions, allowing companies to operate with extreme heat or in lower conditions. If that wasn’t enough, rotary screw compressors also work in areas where other tools might be prohibited.
- Rotary screw compressors are also easy to maintain because they don’t have as many air compressor parts that require maintenance. Believe it or not, a lot of rotary screw compressors lower a lot of maintenance costs because they have 70% less parts than other machines.
- They can also generate more power than some traditional tools. With such consistent and high rates of air flows, equipment runs better and more effectively.
- Rotary screw compressors also conserve energy since they generate less heat than other kinds of air compressors or other machines. They also use less oil than oil-based compressors.
- They run quietly in spite of their consistent air flow. Many of them are built with noise-dampening technology
- Compared with many other machines, rotary screw compressors are not big in size and can basically be stored anywhere.
- Rotary screw compressors will last a long time and don’t easily lose their capacity for efficiency.
While air compressors tools can be incredibly efficient, it’s important for companies to manage compressor lubricants regularly. Lubricant fluid has many functions to keep compressors running correctly. This fluid seals the compressor to prevent leaks and helps maintain a proper temperature. With proper maintenance, compressors can run for many years and contamination of that fluid can be avoided.
If a compressor isn’t functioning correctly, it’s best to find a company that can do an oil analysis. That company will check the compressor oil for oil health, viscosity, water and other contaminants which may be the source of any malfunctioning. Companies must monitor any contamination, especially when ultra fine solids and acids are involved. In fact, acids are the No. 1 reason compressor fluids needs to be replaced and are at the root of issues such as oxidation, residual contamination from a previous oil fill and ingestion from the atmosphere.
When it comes to compressor oil analysis, there are several categories:
- Viscosity: Managing oil viscosity is paramount when it comes to making sure compressors function properly. Lubricants come in contact with a lot of thing when machines are running for manufacturing and viscosity can be affected by any number of things. Regardless of what affects the viscosity, over time it can affect the temperature control of the compressor as well as the ability to properly lubricate all the parts that need lubrication. As a side note, a increase in viscosity within 10% is considered to be a normal range.
- Oxidation: Oil foams expose compressor fluid to air and that lowers viscosity by causing oxidation.
- Dilution: This happens when lubricant fluid comes in contact with gas. Once again, it’s another thing that can lower viscosity.
- Bubbles: Bubbles pop up as oil form churns in a compressor, which also causes a decrease in viscosity.
Companies who do a monthly compressor oil analysis can save themselves from a lot of hassle in the long-term. This analysis will keep companies abreast on the health of the oil as well as the compressor and drastically reduce the chance for unexplained or unexpected failures. The last thing companies want is malfunctions and shutdowns during heavy business times and analysis and maintenance can ensure that doesn’t happen.