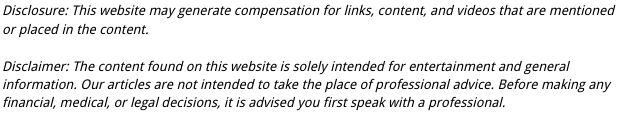
Many companies decide to uproot their facility for expansion purposes, which is extremely taxing and stressful for both the company and its employees. When a company decides to relocate, they’re responsible for ensuring every employee is properly placed and all operations are still running at an optimal level, especially civil engineering management. There are various methods, businesses, and energy facilities use for consolidation and expansions. This includes scheduling and building developments and monitoring for the biggest civil engineering companies in the world, building selection, pavement evaluation, planning, and options analysis, budget supervision and adherence through negotiation and problem solving, and full or global project management and coordination of architects, vendors, and construction teams.
Through the various methods of operations, specific assessments include global capacity strategic planning, pavement evaluation, facility and structural design, and documentation the manufacturing plant floor plan including critical design assumptions, goals, and project constraints that closely follows potential opportunities for improvements such as short and long-term project goals that are given to factory layout consultants. Typically, urban development and pavement evaluation are shared with factory layout consultants to review and further detail state layouts, process descriptions, and capital investment plans for ease of execution and project management. When a civil engineering company relocates, there’s usually a process to maximize efficiency and revamp their old pavement evaluation. Typically, a change of workflow is targeted—an efficient layout provided by factory layout consultants, and other materials to significantly reduce labor and inventory while improving customer service.
Plant Layout
The design process for companies strongly encourages and reinforces client participation through engagement and building development. There are certain requirements factory layout consultants must meet to begin the execution of the proposed space, such as pavement evaluation and aerial lidar and digital imaging services. There are allocated consultants that facilitate the selection of an appropriately sized site and building based on the company’s programming need and growth expectations; factory layout consultants create detailed layouts and based on their amount of workflow, pavement evaluation, and operational optimization. For a company to effectively implement a project, it requires collaboration, planning, and hands-on involvement, especially for large-scale projects. There are proven methods and reliable tools for factory planning, including:
Value stream analysis and value stream design
1. Methods Time Measurement (MTM)