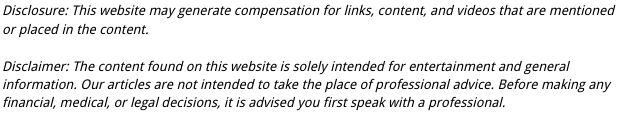

Not all heating is created the same. As an engineer you need to stay privy to the best resources around in order to give and take in equal measure.
Brazing machinery was introduced decades ago and has only continued to evolve both functionally and financially in response to demand. Manufacturers want to save as much money as possible when supplying their engineers, but the omnipresent fear of losing out on quality can keep many from making the plunge from one brand to the next. Aluminum brazing with induction is best done not just by reading the latest journal, but possessing a fundamental understanding of the process. With a little extra knowledge by your side you can ensure no matter where you go, quality will follow.
What Is Induction Heating?
The function of induction heating and brazing machinery is to fully connect one metal to another, creating a seamless transition that can be relied on for any number of simple to complex products. The filler metal is used as a sort of ‘glue’ to keep the primary materials in place, always involving a lower melting point to make sure the transition is flawless. These basic principles have been applied to worldwide manufacturing processes since the 1920’s, ensuring that brazing machinery is never lacking when it comes to innovation and application.
What Are The Primary Parts For A Heat Inductor?
Brazing copper to steel is only possible when all parts are working in tandem. Your average induction heater will typically be composed of the power unit, the work head and the work coil. Induction heating can be used for processes involving temperatures as low as 212 degrees Fahrenheit and as high as over 5,000 degrees Fahrenheit. The two biggest benefits of heating with induction tools is the eddy current heating as well as hysteretic heating. It’s this subtle difference and more that ensures the products we know and love today remain possible.
Which Metals Benefit The Most From Induction Heating?
Each form of metal has its own unique properties. Some are better for everyday appliances, while some are used nigh exclusively for massive projects such as construction or repair. Materials with a high permeability (anywhere from 100 to 500) are the easiest for brazing machinery to use. Iron alloys, in particular, are considered perfect for induction heating for their inherent ferromagnetic nature. Metals are highly malleable and experience extreme fluctuations in their potential with every temperature rise and dip, all of which shouldn’t be neglected if you want to maintain quality.
What Other Metals Benefit From Brazing Machinery?
Carbide tipping and the copper annealing process all need to be carefully monitored if you’re to get the most out of their unique qualities. Silver is frequently used for induction brazing due to its very low melting point. Silver-copper eutectic brazes have melting temperatures as low as 1,100 degrees Fahrenheit and as high as 1,600 degrees Fahrenheit. A temperature at which specific magnetic materials experience a significant shift in their magnetic properties is known as the Curie point. The Curie point of iron, for example, is just over 1,400 degrees Fahrenheit.
What Should I Look For In Applications For Induction Heating?
Brazing machinery is a blend of the old and the new. Your application will benefit greatly from the addition of induction heating provided you follow these simple steps. Keep in mind the characteristics of the part itself (do they have a high melting point or a fickle one that needs a close eye) as well as the design of the inductor. The capacity of your power supply must always be a major factor to make sure you don’t run out of juice mid-project. Lastly, the amount of temperature needed for each application depends on the metal being used and the function of the end product.
Brazing machinery is only as good as its engineer. That doesn’t mean you shouldn’t find the best of both worlds and merge them together.