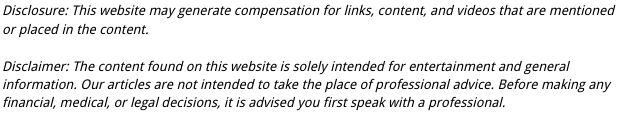
The metal forging industry is a vast one, and metals are essential for modern construction. Steel, aluminum, copper, and a fantastic variety of alloys are critical for making everything from chemical plant valves to jet engine parts to car rims, and the sheet metal industry is due to see some growth in the coming years. But there is more to it than just buying wholesale sheet steel; it all has to come from somewhere, and foundries with induction furnaces are the key. Today’s induction melting furnaces can efficiently melt down metals and remove impurities, and induction heating equipment can be conveniently bought from induction furnace manufacturers across the nation. Better yet, these induction furnace manufacturers often provide installation and repair suggestions and help, so the customers can get all their new gear set up just right for work.
The Business of Metal
The prices of wholesale steel melting furnaces and the like are well justified, seeing how strong the steel and metal market is today. The sheet metal industry is worth billions, and the Bureau of Labor Statistics is confident that this market will see even more growth in the coming years, adding a few thousand new jobs along the way. The United States also imports and exports a lot of steel, and it gets most of its imported steel from Germany, China, and Canada. In fact, Canada alone provides 17% of imported steel, and most of the steel that Canada exports goes directly to its southern neighbor. As for uses, about half of the globe’s steel goes straight to construction and infrastructure, such as I-beams, and about 13% of the world’s steel is used for the automotive industry. Another 16% of it is used to make mechanical equipment, such as for making robotic arms and automated systems.
Steel can be hot rolled, and that’s used to make I-beams and railroad tracks. If the hot rolled steel is passed through rollers again but at room temperature for that second pass, the result is cold rolled steel, which boasts precise dimensions and a protective finish (so it’s ideal for manufacturing). Meanwhile, aluminum has a role to play, being a lightweight and flexible metal. Often, it is used to help make vehicle bodies lighter and therefore more fuel efficient, and aluminum is used to make power cable wires (copper is too heavy), and it’s also used to make mobile electronic device parts (since plastic is too fragile and steel is too heavy). Finally, alloys are made from ingredient metals such as steel, aluminum, copper, brass, and nickel, and they are designed for extremes of pressure, heat, cold, or corrosion that regular steel or aluminum can’t handle. Imagine undersea pipes (exposed to salt water), or the plating on the space shuttle.
Forging Metals
No matter what steel or aluminum is used for, though, it first has to be forged. Many of today’s foundries make use of induction furnaces, which feature electrically heated filaments to melt raw iron and other materials, or to recycle scrap steel or aluminum. This is a clean and efficient process when compared to older methods, and the furnace’s coils and electrodes are made of tough metals like tungsten, so they don’t accidentally melt themselves. These furnaces and their parts are tough, and often feature alloys, but they will still sometimes need repair or replacement.
When a new foundry is opened, for example, the owner will look up local induction furnace manufacturers and buy some wholesale parts, and have them shipped and set up. If in-house labor can’t handle this, then staff from the induction furnace manufacturers will help install the machinery, and calibrate it all and advise the owners on how to operate it correctly. Also, these induction furnace manufacturers can be contacted later on if the owners need to order some new spare parts, such as if a tungsten electrode went bad, or if an older machine should be replaced with newer and better model. But more often, it is consumable parts that the owner will buy from local induction furnace manufacturers, since induction furnaces are typically designed to be low maintenance and have relatively few troubleshooting needs. This makes them convenient and cost effective to own and operate.