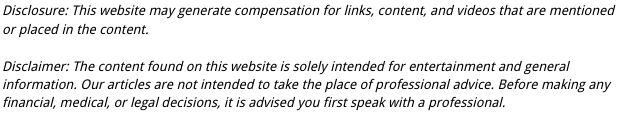
The expansive growth of industrial sectors globally has led to the development of innovative materials to meet the increasing demands for efficiency and productivity. One such advancement is the utilization of ceramic inert support media. These materials are rapidly gaining importance due to their versatile applications and exemplary properties such as thermal resistance, mechanical strength, and chemical inertness.
The rising trend in incorporating these media into industrial systems showcases a paradigm shift towards more efficient and sustainable operations. With global industries striving for more environmentally friendly approaches, the demand for robust and reliable materials such as ceramic inert support media is only expected to rise. Let’s explore the specific applications and benefits that these innovative materials bring to diverse industrial domains.
Catalytic Processes
Ceramic inert support media play a critical role in catalytic processes, which are vital for numerous industrial operations. Their use in these processes primarily springs from their ability to provide a stable environment that enhances catalyst performance. By serving as a substrate, these media enable the proper dispersion of catalytic materials, thus maximizing reaction efficiency and throughput.
The petrochemical industry extensively utilizes ceramic inert support media to improve the efficiency of catalytic converters, which are crucial in transforming crude oil into useful products. These media ensure optimal surface area and support conditions for catalysts, significantly enhancing the conversion rates. Furthermore, their thermal stability allows for sustained operations under high-temperature conditions, further affirming their indispensability in catalytic applications.
In the chemical manufacturing sector, ceramic inert support media are integral in processes that involve synthesis and processing of chemicals. The media’s resistance to chemical corrosion and thermal shock makes them ideal components in various catalytic sequences. Thus, adopting ceramic inert support media in catalytic processes not only boosts the performance of industrial systems but also contributes to extended operational lifespans.
Gas and Liquid Filtration
Another significant application of ceramic inert support media lies in gas and liquid filtration processes. These media are renowned for their exceptional filtration capabilities, ensuring the removal of contaminants to achieve high-purity outputs. Their use in filtration is primarily attributed to their porous structure and mechanical strength, which enable them to withstand harsh operating conditions.
In the environmental industry, ceramic inert support media are employed in air filtration systems to remove particulate matter and other pollutants. Their ability to withstand high temperatures and resist chemical degradation makes them an essential component of industrial exhaust systems. This functionality is critical for industries concerned with minimizing their carbon footprint and adhering to environmental regulations.
Water treatment facilities also benefit significantly from ceramic inert support media, using them in filtration systems to purify drinking water and treat wastewater. These media effectively capture impurities, ensuring safe and clean water for consumption and reducing environmental harm. Therefore, the industrial adoption of ceramic inert support media in filtration systems underscores their role in promoting sustainable environmental practices.
Support Structures in Chemical Processing
Ceramic inert support media are further employed as structural supports in various chemical processing applications. Their robustness, combined with their lightweight nature, makes them ideal for constructing support structures that are stable yet easy to manage and transport. These characteristics are especially beneficial in the design and implementation of packed bed reactors and other related systems.
In the realm of chemical processing, packed bed reactors are pivotal in conducting catalytic reactions efficiently. Ceramic inert support media provide the necessary structural stability and distribution uniformity required for optimal operation. These support structures maintain the integrity of the reactor’s internal environment, enabling precise control over reaction parameters and product quality.
The inertness of ceramic support media ensures minimal interaction with process reactants and by-products, thus preserving the purity and efficiency of chemical reactions. As industries continue to seek higher levels of precision and performance, the role of ceramic inert support media as structural supports becomes increasingly prominent. Their application ensures that chemical processing infrastructures are both reliable and effective in their operation.
The continued evolution of industrial technologies demands materials that can withstand rigorous conditions while maintaining high performance levels. Ceramic inert support media meet and exceed these requirements, providing industries with reliable solutions that boost productivity and ensure compliance with environmental standards. As global industries navigate the complexities of 21st-century demands, the relevance of ceramic inert support media becomes increasingly apparent.
.