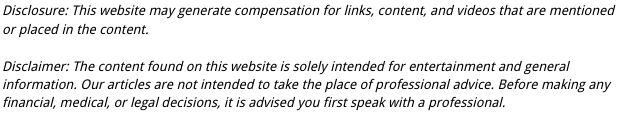
Factory maintenance planning and scheduling are essential processes that help manufacturing plants operate efficiently by minimizing equipment downtime and ensuring the longevity of machinery. These processes are designed to anticipate equipment maintenance needs, allocate resources effectively, and ensure that repairs and routine services are carried out without disrupting production schedules.
The Role of Maintenance Planning
Maintenance planning is the first step in the process. It involves identifying the maintenance tasks that need to be performed on factory equipment to prevent breakdowns or address ongoing issues.
The maintenance planner works closely with the production team to understand the operational demands of the factory, as well as the maintenance needs of machinery. This allows them to develop a comprehensive plan that outlines which tasks need to be completed, when they should be done, and what resources are required.
During the planning stage, the type of maintenance—whether preventive, predictive, or corrective—is determined. Preventive maintenance is scheduled at regular intervals to prevent breakdowns, while predictive maintenance uses data and condition monitoring to anticipate when repairs might be needed. Corrective maintenance, on the other hand, addresses any unforeseen issues as they arise.
Scheduling the Maintenance Tasks
Once the maintenance plan is in place, the next step is scheduling. This involves determining the most convenient time to carry out maintenance tasks while minimizing disruption to production. The maintenance schedule needs to align with the production calendar, taking into account busy periods or planned shutdowns. Schedulers must consider factors such as the availability of personnel, spare parts, and equipment downtime windows.
A good maintenance schedule prioritizes tasks based on urgency and importance. Critical machinery that could halt production if it fails is usually scheduled for maintenance during planned shutdowns or times of low production. Less critical tasks may be slotted in during periods of routine operations.
Tools and Technology
Many factories now use Computerized Maintenance Management Systems (CMMS) to manage maintenance planning and scheduling. These software tools can track equipment health, alert maintenance teams when service is due, and ensure that work orders are completed on time. With predictive maintenance, sensors and data analytics are used to monitor equipment performance in real time, allowing the maintenance team to make informed decisions about when to perform necessary work.
Benefits of Effective Maintenance Planning and Scheduling
When properly executed, maintenance planning and scheduling improve overall factory efficiency. Equipment runs more smoothly, breakdowns are reduced, and production downtime is minimized. This ultimately saves the factory money, enhances safety, and boosts productivity, ensuring that the facility can meet its operational goals while keeping machinery in optimal condition.
Watch the video above to learn more about factory maintenance!.