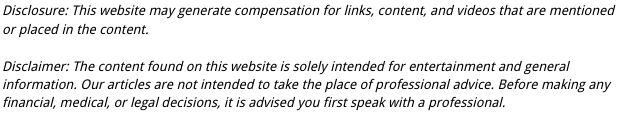

Plastic is a very popular material. It has been estimated that about 2.5 million plastic bottles are used each hour in the United States. Every year, nearly 600 billion pounds of the material is made and used around the globe. This is only increasing as the demand goes up by about 5% each year. The plastics industry is the third largest American industry at the moment. In 2013, that industry made about 107.5 billion pounds. Colored plastic bottles are popular for a number of uses around the planet. The process to make things as colored plastic bottles is uniform and is fairly straight forward. Here is a look at how these useful items are made:
Step 1: The process by which plastic bottle containers are made is called the extrusion blow molding process. The plastic bottle manufacturer will take plastic pellets and add them to a blow mold. The mold is then heated so that the pellets melt.
Step 2: The melted plastic is placed into a parison, which is a tube of plastic. The parison, and the plastic inside will be then cut to be the right size.
Step 3: The parison needs to be reheated to go into a second mold. The second mold is the right shape, for example, the colored plastic bottles for Coke products have a very distinctive shape. When these soda bottles are made, the second mold has that distinctive shape. This mold also has the correct top. Most colored plastic bottles have screw tops and the second mold also has that feature.
Step 4: Pressurized air is forced into the mold. This will force the plastic material to coat the walls of the mold. When the high temperature meets the high pressure of the air, the result is that the molecules of the plastic are polarized. They will crystallize on the walls of the mold and the product that is created is very strong and durable. The timing of this step is critically important. If it is not timed correctly, the colored bottles will have the wrong shape.
Step 5: The bottom is added to the colored plastic bottles. The bottom of plastic bottles has a concave shape. This allows the bottle to stand up right. This is not a process that can happen until after the walls of the bottle have been set. At the end of the blowing process, a bottom is added to the bottle mold.
Step 6: After the plastic has been molded into the right shape and the bottom has been added, the plastic bottle company will cool the mold. There are several ways this can be done. Some plastic bottle suppliers use liquid carbon dioxide to cool the mold. Others use water that can be poured on the mold. Others will shoot room air or moist air that has been pressurized to cool the mold. No matter what the method used is, this step needs to be done quickly in order to keep the bottle at the right shape. It is easy to do this too slowly and not get the right shape for the bottle.
Step 7: The last step is to take the bottle out of the mold. When this is done on an assembly line type situation, the bottles are all made continuously. They are all attached to each other and as they are made, they are cut off the line and then trimmed to be the right size. There are also other imperfections that need to be dealt with during this process. It has been estimated that imperfections in plastic bottles costs the companies about one quarter of the plastic that is used. The good news about that is that it can be recaptured and used again.
Many people around the world will balk at the use of plastic for a wide variety of reasons. The main one is they worry about the environmental impact. What these people do not realize is that using colored plastic bottles can save energy and transport more with less. It takes far more glass, for example, to transport liquid than plastic. Most people have access to plastic recycling so using the material can be a lot better for the planet than many people often realize.