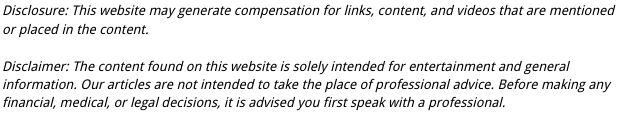
Modern industry involves moving a lot of gases and liquids in factories, refineries, and plants, and that requires having the right pipes, nozzles, pumps, and valves for the job. Industries as varied as breweries to dairy farms to pharmaceutical processing plants make use of coil pipes, stainless steel storage tanks, chemical holding tanks, and more to keep fluids moving properly. Such hardware may be under great pressure or contain corrosive or dangerous materials, so a coil pipe or valve must be made from the correct materials for the job. And of course, a factory owner should have coil pipes, valves, regular pipes and storage tanks, and more routinely inspected for faults. Faulty coil pipes or other hardware should be replaced at once.
Coil Pipes
These coil pipes are specialized pipes built in a spring-like shape, and this allows them to draw up material when they are compressed and then released. Often, oil industries make good use of these coil pipes, and such pipes are not liable to leak or suffer from joint problems since they have no joints at all. They can draw up liquids where other pipes may suffer from the effects of gravity, ensuring that they’re a staple in many industries. Such pipes may be formed by wrapping raw metal around a tube to form their distinctive coil shape, and they may be made from different materials such as steel or copper, depending on how they will be used. These coil pipes can even be used to collect boiling alcoholic liquids and condense it elsewhere, creating a more pure product. In other cases, such coils are used for the pressure that they exert when they are compressed and released, providing physical work rather than carrying liquids inside. These are industrial-scale springs.
Liquid Storage and Processing
Meanwhile, many processing plants and refineries today are using chemical storage tanks, stainless steel pressure vessels, pumps, and valves to move and store liquids. As mentioned earlier, the contents of these pipes and tanks may vary among water, milk, pharmaceutical chemicals, oil and natural gas, and soft drinks, among others. These different pieces of hardware can be bought wholesale and installed when a plant is being built, and faulty hardware may either be replaced with new parts or repaired to fix leaks. An expanding refinery plant may need new pipes and storage tanks to hold all this growth.
The materials used for pipes, storage tanks, and even pumps and valves makes a real difference. Some materials such as plain water and milk are low-intensity contents, so mere plastic can be used to move and store them. A pump in a dairy or milk processing plant, for example, may have tough but lightweight and affordable plastic pumps in it, and the same is true of water. Turbine-based, plastic pumps may have only limited power since these liquids are viscous and easy to move. The same may be true of the valves found in these pipes and the storage tanks.
Other contents are more demanding, however, and mere plastic or even stainless steel might suffer. Pharmaceutical chemicals are strong and corrosive, and would damage pipes or storage tanks made from the wrong materials. Instead, specialized metal alloys will be used to build the tanks, pumps, valves, and pipes for these contents. Metal alloys are composites made from two or more “ingredient” metals, and the exact metals used, and their ratios, will be engineered for specific jobs. Metals such as steel, copper, nickel, titanium, and others may be found in these metals. Such metals may be designed to endure extremes of acidity, heat or cold, pressure, and more. In fact, the external material may be designed this way too, such as pipes found underwater. Such pipes face constant corrosive pressure from salt water and must be built accordingly. And if the liquids being moved are dense and thick, a stronger pump motor will be needed to move it. Weaker pumps would burn themselves out trying to move those contents.
But even the right materials may fail sometimes, so routine inspections and repairs should be done to keep hardware in good shape. Otherwise, leaks may damage the premises and result in the expensive loss of materials. Pumps with burnt-out motors can be replaced, and malfunctioning valves can be repaired.