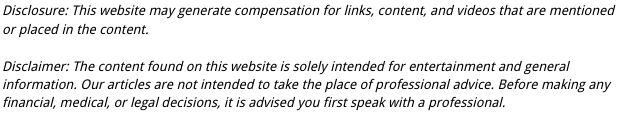
Finishing Systems
When it comes to metal finishing being able to finish large quantities at once is referred to as “mass finishing”. This process is used for burnishing, and deburring, as well as polishing the metal components. Two of the most common types of this finishing are vibratory and barrel finishing. While both have their pros, here we’ll be focusing mainly on vibratory finishing, and the use of vibratory deburring machines.
The Use Of Vibratory Machines
The vibratory finishing process involves the use of specialized deburring machines; a mr deburr is one of the most common types of this machine. Parts and compounds are put into the vibratory tub, which then uses a vibrating force to create friction between the parts inside. As the components grind against each other they become polished. This allows for a mass quantity of components to undergo the deburring process at once, which helps boost overall productivity.
The Vibratory process can be used for a variety of mass finishing. These include:
- Cleaning.
- Polishing.
- Descaling.
- Surface Prepping.
Machines like the mr deburr allow for a cleaner deburring process that can’t be replicated by handheld methods.
The Vibratory Process
When using a mr deburr machine, the tumbler is filled with chemical compounds and a vibratory polishing media. These aid in the deburring process, and help ensure the best finishing result. Water may also be introduced as an additional lubricant and cleaning application. Once components are introduced to this solution the vibrations create a circular rotation within the machine, this causes components to grate against each other and as such achieve a polished finish at the end of the process.
This type of finishing tends to be more popular in the metal finishing industry, as it produces consistent results, and can be used for a variety of component sizes, from large and sturdy to small and delicate. Vibratory finishing is also known to produce an overall smoother finish with less wear to the surface of components. This helps keep polished components lasting longer when put into use.
Vibratory machines, like the mr deburr, do tend to be more complex than barrel finishing; however, they take less time to produce a finished result when compared to barrel finishing machines. Likewise, barrel finishing tends to run the risk of surface denting, due to the fact that components ‘tumble’ around the machine and into one another, as opposed to grinding against each other.
If you are in need of deburring it’s worth looking into metal finishers near you that specialize in the vibratory process. Additionally, if you are looking into getting into the industry, learning this process is a good first step, and can help you exponentially as you are starting out.